W dzisiejszym artykule przedstawię proste wskazówki jakie należy wziąć pd uwagę podczas projektowania pod druk 3d. Poruszę kwestie dotyczące rozmiaru, orientacji elementu na platformie, stosowania podpór oraz tolerancji wymiarowej.
Rozmiar
Wielkość ostatecznego elementu nie ma znaczenia ze względu na to, iż każdy model można podzielić na jego składowe części. Ograniczeniem w tym przypadku będzie przede wszystkim przestrzeń robocza drukarki. To ona zdeterminuje maksymalną wielkość poszczególnej części modelu. Im mniejsza przestrzeń robocza tym na mniejsze elementy musimy podzielić nasz model. Projektant musi wziąć pod uwagę w jaki sposób elementy te będą ze sobą łączone i odpowiednio zaprojektować miejsca łączeń.
Zasadniczo możemy wyróżnić dwie możliwości łączeń. Części możemy połączyć ze sobą klejem lub połączyć śrubami. W każdym z wymienionych przypadków należałoby zaprojektować łączenia w taki sposób żeby ułatwiły końcowy i poprawny montaż. Przydatne będą tu odpowiednie elementy pozycjonujące jedną część w stosunku do drugiej.

Inaczej ma się sprawa do modeli o niewielkich rozmiarach. W tym przypadku wybór technologii ma znacznie większe znaczenie. W przypadku technologii FDM minimalny rozmiar elementu czy też detalu na danej części będzie determinowany przez średnice dyszy drukującej (o tym więcej w dalszej części artykułu). Przy druku niewielkich, szczegółowych elementów lepiej spisze się technologia SLA (przegląd technologii przyrostowych).
Orientacja
Odpowiednia orientacja modelu w procesie drukowania wpływa na jego wytrzymałość mechaniczną oraz na jego estetykę. Technologie przyrostowe mają to do siebie, że drukowany obiekt ma cechy anizotropowe. Wydruki posiadają różną wytrzymałość w różnych kierunkach działania siły. Najmniejsza wytrzymałość występuje równolegle do warstwy wydruku.
Jak sobie z tym radzić? W miarę możliwości projektować tak części aby powierzchnie równoległe do płaszczyzny wydruku były jak największe. Zastosowanie odpowiedniego materiału oraz temperatury również wpływa na aspekt wytrzymałościowy drukowanego elementu, ale to dotyczy już samego procesu wydruku i doboru odpowiednich parametrów.
Podpory (Support)
Jedną z zalet druku 3d jest możliwość wytwarzania w łatwy i przystępny sposób skomplikowanych brył oraz struktur. W zależności od skomplikowania modelu 3d, może być konieczne użycie w procesie druku tzw. struktur podporowych (support). Jednakże, projektant podchodząc do projektu, powinien starać się niwelować obszary wymagające stosowania podpór. Stosowanie supportu wpływa przede wszystkim na czas wydruku, zwiększa zapotrzebowanie na materiał oraz dodaje dodatkowej pracy którą trzeba wykonać w procesie odseparowywania materiału podporowego od reszty wydruku. Oczywiście to wszystko wpływa na zwiększenie kosztów wytworzenia danego elementu.
Możemy mówić o dwóch sposobach na generowanie podpór. Jednym z nich będzie generowanie supportu automatycznie przez specjalistyczne oprogramowanie typu slicer natomiast drugi sposób będzie dotyczył ręcznego wymodelowania podpór w odpowiednich, koniecznych miejscach projektowanego modelu. Zaletą takiego podejścia jest mniejsza ilość supportu niż w przypadku struktur generowanych automatycznie.

Jak niwelować konieczność wykorzystania struktur podporowych? Przede wszystkim starajmy się ograniczać obecność nawisów w modelu. W ramach możliwości stosujmy łagodne przejścia odchylone o 45° od pionu (rys. 3). Możemy również tak zaprojektować część aby zamiast supportu móc wykorzystać metodę mostów (rys. 4). Stosowanie mostów jest jednak również ograniczone. W większości przypadków sprawdzą się mosty do długości max 4 – 5 cm. Powyżej wspomnianej odległości, struktura taka będzie za bardzo opadać. Pisząc ogólnie, nie da się drukować w powietrzu.

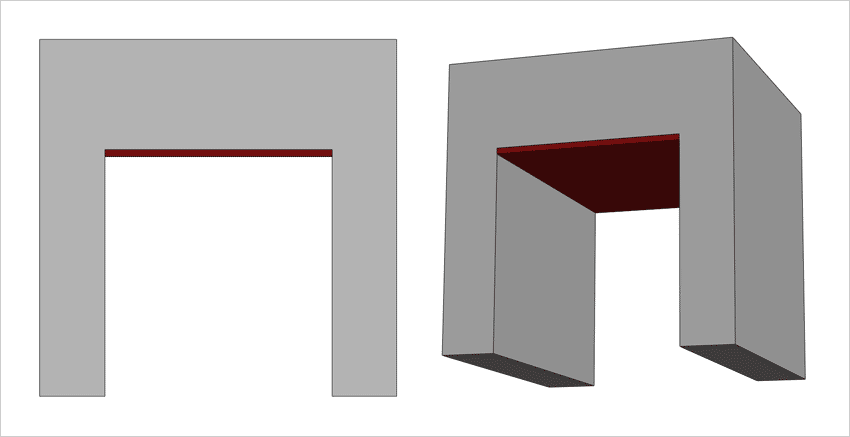
Tolerancja wymiarowa
Ostatnim ważnym elementem jaki należy wziąć pod uwagę podczas projektowania pod druk 3d, jest aspekt dotyczący tolerancji wymiarowej. W przypadku druku 3d musimy wziąć pod uwagę możliwości fizyczne maszyny oraz skurcz materiału.
W przypadku technologii FDM podczas projektowania, należy wziąć pod uwagę średnice dyszy urządzenia, gdyż ta będzie determinować wielkość najmniejszego detalu. I tak np. w przypadku szerokości ścianek projektowanej części, należało by stosować wielokrotność średnicy dyszy. Standardowa średnica dyszy w urządzeniach typu FDM wynosi 0,4 mm. Jeśli chodzi o minimalną szerokość ścianek to nie powinna być ona mniejsza niż 0,8 mm.
Projektując część należy uwzględnić również skurcz materiału. Ma to szczególne znaczenie w przypadku pasowania, łączenia kilku części ze sobą. Dobrą praktyką w tym przypadku będzie zastosowanie luzu między częściami od 0,3 do 0,5 mm. Ta sama zasada dotyczyć będzie otworów, które pod wpływem skurczu mają na ogół mniejszą średnicę niż zakładał projekt.